5 Reasons To Add Reality Capture and Digital Twins to Your QA/QC Process
Learn how you can revolutionize your workflow
In the construction industry, quality control and quality assurance (QA/QC) play a crucial role in ensuring that projects are completed safely, efficiently, and to the highest standard. Adopting new technologies and processes is key to improving the QA/QC process and keeping up with evolving industry standards. One technology that has proven particularly valuable in this regard is reality capture, and it can come in many different forms.
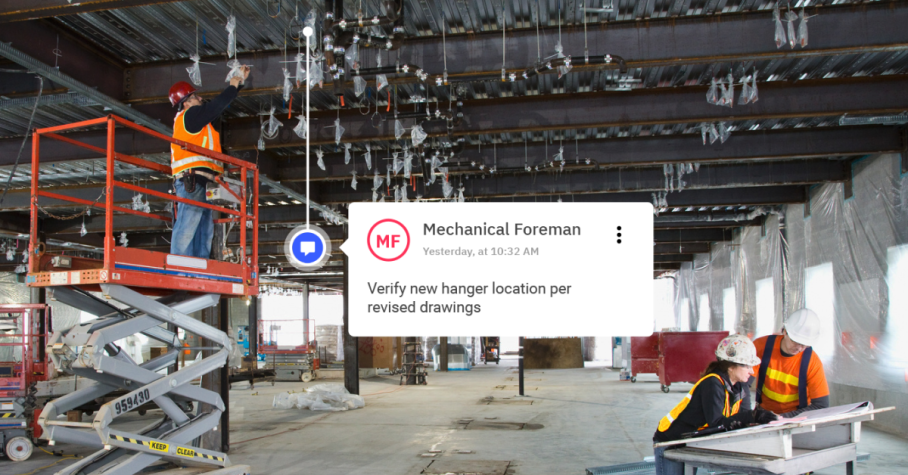
What is reality capture, and why should you adopt it?
Reality capture is a process that involves scanning a building or job site to gather visual and detailed data about existing structures or sites using technologies such as 3D laser scanning for construction with lidar and photogrammetry. This data is then used to create digital twins, 3D models, and BIM files. By utilizing reality capture, architects, engineers, and construction professionals can enhance communication, reduce errors, minimize rework, and improve overall project efficiency, ultimately saving time and resources.
What is a digital twin, and how is it different from reality capture?
Reality capture is the technology and process of scanning a building. The output of reality capture in construction is typically a digital representation of the job site, referred to as a “digital twin”. Using Matterport digital twins for construction, you can virtually walk through a job site like you would with Google street view, and export 3D data in point clouds or 3D mesh files. Digital twins can be hosted securely in the cloud, accessible without installing specific software.
Here are five reasons why you need to add reality capture and digital twins to your QA/QC process:
1. Ongoing Documentation and Comparison of 3D Model to As-Built Conditions
Reality capture technology, which involves creating 3D models or point clouds of physical spaces, allows you to document a construction site at different stages of completion. By comparing these scans to the 3D design intent model of the project, you can identify any discrepancies between the design and the as-built conditions early on, enabling you to make quick and informed decisions. This is exactly why it is important to conduct as-built surveys during projects, to ensure precision and accuracy throughout.
2. Reduce Site Visits with 24/7 Access to Job Site
With the tap of a link, you can remotely access a job site at any time, reducing the need for physical site visits. Matterport allows you to take measurements, make annotations, and inspect the site from your desk, providing the clearest virtual experience of a job site to save valuable time and resources instead of visiting the physical location.
3. Remove Distractions of the Job Site with Remote Inspections
Remote inspection is an important aspect of reality capture technology. It allows you to take a closer look at a site without being physically present, reducing the distractions of the ever-changing job site and letting construction continue while you QA/QC remotely. This means you can check for compliance with standards and specifications without interrupting the workflow.
4. Less Miscommunication with Photorealistic 3D Scans
When communicating details to stakeholders, it can be challenging to convey complex information accurately. By referencing a pinpoint on a photorealistic 3D scan with a Matterport digital twin, you can eliminate any miscommunication and provide a clear and precise understanding of the issue at hand. This visual clarity leads to better collaboration and a more accurate representation of the facts.
5. Better Collaboration by Bringing the Visual Site Context to Your Issue and RFI Workflow
Reality capture and digital twin technology like Matterport help to bring the visual site context to your issue and RFI workflow, creating a more collaborative process. Scan a job site with Pro3 to generate photorealistic imagery, 3D models, and point clouds of construction sites that can be used to facilitate communication and collaboration among teams. Try integrations with Autodesk Construction Cloud, making it easier for teams to work together with one source of truth and make informed decisions quickly. In conclusion, reality capture technology can revolutionize your QA/QC process by providing continuous documentation of the project, reducing the need for physical site visits, removing distractions of the job site, eliminating miscommunication, and facilitating better construction collaboration. By incorporating reality capture into your QA/QC process, you can improve the efficiency and accuracy of your construction projects, ultimately saving time and resources. Register for our webinar on Digitizing your QA/QC Workflow to get a detailed look into the phases to capture and best practices.