Facility Management Process Steps & Real-Life Examples Of Efficiency Gains
Facility Management Process: 5 Steps To Improve Efficiency
Maintenance, inefficient processes, unplanned downtime, poor energy efficiency—countless things keep facility managers up at night. But, the right facility management process will help you streamline facility operations, effectively coordinate with facility management teams, prevent breakdowns, and more.
In the past, many facility management processes neglected the role of technology. With effective use of modern tech, including a digital twin platform, you can not only master facility management but get more out of your facility management processes than ever before.
What is a facility management process?
A facility management process is anything that falls under the umbrella of facility management as a whole. Facility management processes can entail:
General facility maintenance
Business continuity planning
Space management and space utilization planning
Physical asset management and tracking
Fire safety audits and planning
(Preventative) maintenance planning and scheduling
Emergency preparedness
Energy consumption and energy efficiency management
Project management and team communication
Risk management
Overseeing building systems, including HVAC systems, electrical, lighting, etc.
All of the above facility management processes play a larger part in your overall facility management strategy. Make sure you’re up to date on proper facility management strategies as well, as this can help you drive down operating costs, bolster preventive maintenance, and improve employee safety.
Without the right facility management process, you’re more likely to find yourself in a reactive state. Maintenance issues, like critical equipment failures, can occur more often. Safety audits can cause panic and last-minute planning. Inefficient space utilization and workflows can hurt productivity and the employee experience. Any of these issues on their own is a hindrance, and together they can cost your facility a significant amount of time and money.
4 pillars of facility management
Facility management encompasses a lot. To simplify things and make the process more manageable, facility management is typically broken into four pillars, each one playing a critical role.
1. People
People are at the heart of effective facility management. Successful facility management includes spearheading employee initiatives that improve overall well-being, foster a more welcoming work environment, talent acquisition, optimizing people-based workflows, and more.
It’s true facility managers have to ensure the overall success of the facility itself. But, without happy, productive team members, everything else comes to a screeching halt.
2. Processes
Happy people can only go so far if processes aren’t set up for operational efficiency and safety. Process management includes analyzing current workflows and processes to find inefficiencies and safety issues. It also entails making sure processes are setting employees up for success. For example, if you have some remote workers, processes need to effectively accommodate this by establishing clear remote work policies and ensuring access to the necessary digital tools.
Equipment maintenance is another core element of the process pillar. Ensuring you and your team have a regular maintenance schedule can ensure the life cycle of equipment is longer, and that maintenance is preventive and not reactive.
Identifying and correcting these can result in more streamlined workflows, more productive and happy employees, and higher profitability for the facility.
3. Place
Next is the place, or building, itself. Proper upkeep and property management is essential to a smooth operating facility. Within the scope of facility management processes, place management activities include space planning and utilization, general upkeep, handling building upgrades as needed, landscaping duties, etc.
Staying on top of this pillar can increase the lifespan of the building itself and help with overall profitability, as well as safety.
4. Technology
Technology is the last, oft-neglected pillar of facility management processes. Facility management used to require tons of manual work, from tracking equipment cycles and maintenance, to manually pacing facilities to determine how workflows can be improved.
Using modern technology, from Industrial Internet of Things (IoT) devices to digital twins, can help you automate workflows, streamline people-powered functions, pull insightful real-time metrics from equipment, and find more time for things like building management.
5 core facility management process steps
There’s no single way to develop an effective facility management process, as every facility and industry is unique, as are the challenges they face. But, there are several steps you can take to get you on the right path. Keep in mind your own facility and industry may bring nuances into the equation that change how this process looks for you.
1. Define facility management objectives
Every facility has unique objectives they’re trying to achieve, whether specific to that location or part of overarching corporate goals. While a facility management process should provide all the benefits mentioned earlier, it also needs to help you with any facility goals.
Involve relevant stakeholders and work together to examine your facility’s current performance.
How’s the overall performance/output for your facility?
What’s your safety record like?
Is there frequent equipment downtime?
How does the facility’s energy consumption look over the past X years?
What does employee retention look like?
Are there corporate goals your facility needs to support?
Asking the above questions can help you check the pulse of your facility as a whole. If your facility is meeting current goals, then focus on the other elements of the list: output, efficiency, downtime, energy, employee satisfaction, etc.
From there, create objectives that help you work toward addressing any pain points or unfulfilled goals. For example, if you have frequent equipment downtime, set goals like “reduce Q1 downtime by 10%” and “schedule regular equipment maintenance” to help you remedy the larger problem.
2. Identify facility needs
Look over your objectives identified in the previous step and ask yourself what you need to fulfill each one. Do you have the people power to make them happen? Is an outside consultancy potentially required?
As you look over needs, don’t neglect the role of technology. Industrial IoT devices can help you automate processes and gain deeper insights into your facility’s performance. If you can’t afford new IoT-connected devices, you can retrofit equipment with IoT sensors and still gain many of the same benefits.
You’ll want to make sure you have the people to support any new technology you plan on bringing in as well. If you’re bringing in a number of solutions, it could make sense to hire a full-time employee who's focused on managing the tech and owning the processes.
3. Create a facility management plan
A fleshed-out plan is core to successful facility management. Develop an in-depth plan that speaks to your facility management objectives and covers:
Maintenance planning and scheduling
Emergency planning and compliance
Safety training
Process/workflow audits and optimizations
Technology implementation and training
Your plan can include far more than what’s listed above. For example, vendor management could warrant its own category, especially if you have a number of vendors and deal with high-dollar orders. As you develop your plan, assign stakeholders who can own each element of the plan and train their teams as needed.
4. Support staff with ongoing training
With all the pieces in place, it’s time to support your staff with ongoing training. New technology, workflows, practices, and keeping up with the market, in general, requires your team to always be up-to-date on training.
Start by training your team on any new technology and workflows, etc. From there, find a training cadence that makes sense for your team and facility. Not all facilities need quarterly training, while others might require even more frequent training.
5. Adjust as needed
No facility management process is set in stone. Monitor your facility’s performance and make changes as you see fit. If maintenance has improved but productivity is down, revisit your workflows and figure out if there are choke points or if people are struggling to use new technology, and so on.
Real-life examples of how digital twins are applied to facility management
Facility management entails a lot. And on top of it all, you have to stay agile to keep up with changing markets and regulations. Fortunately, digital twin technology can help you not only improve your facility management, but also stay more agile than ever. Digital twins accomplish this by providing numerous benefits.
CRB Group increased efficiency and collaboration
In the past, capturing scans of spaces required using time-consuming equipment. A lack of scans altogether meant sacrificing detail, and losing out on the ability to collaborate. With digital twins and modern cameras, like the Matterport Pro3, you can easily scan indoor and exterior areas. This allows you to quickly deliver digital twins to clients or other teams and collaborate about any aspect of the facility online, regardless of location. CRB is a sustainable engineering, architecture, construction, and consulting firm specializing in biotech and pharma. Traditionally their team would visit client sites to plan and begin work.
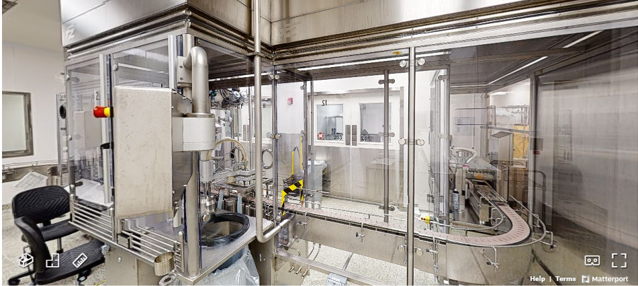
With the adoption of Matterport’s digital twin platform, CRB was able to quickly capture existing conditions for renovations or modifications. This also allowed them to offer even more services than before. For example, a biotech client needed to document a fermentation suite, including pipes, valves, and tube diameters. With Matterport digital twins, CRB was able to scan the entire facility in a single day, then add Tags to detail valve types and proximity to other equipment. From there, they could easily loop in the client and collaborate on the file.
By using Matterport, CRB was able to:
Send one engineer to client sites for scans instead of six to ten
Capture entire sites in one day instead of several
Expedite the design process by three weeks
Cut travel by one-third
“Matterport allows us to communicate more effectively with our clients, stakeholders, and internal teams to develop solutions to address even the most complicated design challenges.”
-Chris Link, regional Virtual Design and Construction Manager, CRB
The University of Wolverhampton gained deeper insight into workspaces
Digital twin technology provides a wealth of information, allowing for deeper insight into workspaces and the ability to maintain accuracy when renovating or performing building maintenance. This is largely due to the speed at which you can take scans using modern tech, like Matterport’s platform. You can easily take scans each day, ensuring the historical data of the site is preserved. With this, you can also keep tabs on construction projects and processes over time, providing updates to stakeholders and keeping everyone in the loop.
The University of Wolverhampton, based in England, has more than 21,000 students each year. The school was recently renovated, which entailed overhauling a 12-acre site that contained a building dating back to 1873. They wanted to preserve history, but also build a state-of-the-art campus for their architectural students.
Using Matterport, the university was able to take frequent scans of the site and ensure no historical details were lost during the renovation. But, the perks didn't end there. The university turned the renovation into a teaching moment, thanks to the detail of the Matterport scans. Using Matterport digital twins, the team at Wolverhampton was able to create virtual tours for students, with the ability to see historical views and notes. This information also helps from a maintenance standpoint, as the team now has detailed visuals and schematics to give technicians.
BMO improved record keeping and reduced travel time
Proper recordkeeping is critical for facilities, whether you’re audited or want to track the progress of your document management efforts over time. This is especially true if you have multiple facilities to manage, as you can’t be everywhere at once. Accurate digital twin scans can keep you and everyone else in the loop, allowing you to digitally tour facilities and make informed decisions on the fly. And, with each scan, comes a rich, 3D record.
BMO is a leading North American bank that has more than 13 million customers. The eighth largest bank in North America by assets, BMO is no stranger to managing multiple locations.
In 2022, they were in the midst of an acquisition, taking on 503 branches from Bank of the West (BOTW). All 503 branches required updates in order to stay consistent with BMO's branding. Without the right technology, this would require an astronomical amount of travel.
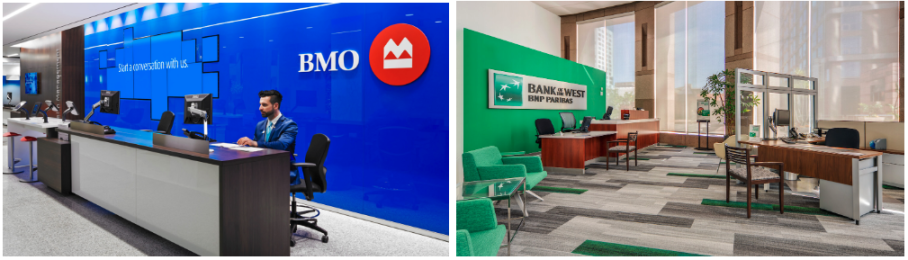
Using Matterport, BMO was able to quickly and efficiently scan each location. Then, BMO design managers assessed each scan and location, checking for brand consistency. This allowed them to note which locations needed to update colors, layout, and more.
BMO also had to determine which locations needed networking updates. The BMO tech team turned to Matterport and used the scans to check server rooms, phone and computer stations, and more. This made it possible to flag locations for updates without having to send tech teams to each location.
In the end, BMO was able to obtain scans of all 503 locations within three months and managed to save 6,000 hours of survey time. And, they have digital scans of each location which they can revisit and keep for records for years to come.
No matter your industry or niche, Matterport can help you capture detailed digital twins and streamline your facility management process.