Smart Buildings, IoT & Digital Twins: Transforming Facility Management with Connected Technology
Large residential and commercial buildings can hold a wealth of unseen data. Unlocking that data enables facility managers to optimize energy management, improve equipment performance, and enhance occupancy management, in real time. Without the right tools, that information remains locked away and unusable.
Enter IoT (the Internet of Things) and 3D Digital Twins. Sensor data and a photorealistic 3D model of your building helps you track and manage everything from air conditioning to asset health. With continuous feedback on building performance and an accurate visual representation of your building, you can quickly optimize building management from anywhere.
Smart building ecosystems are designed to be intuitive and easy to use, which is useful for building managers who want to stay on top of operations without relying on tech experts.
Diving deeper into smart building systems, this article will:
Explore 6 operational benefits of smart buildings powered by the connectivity of IoT and digital twins
Provide real-world examples and use cases alongside measurable results
Give you a practical understanding of how smart buildings work
What is smart building IoT?
When people refer to smart building IoT, they are talking about the sensors and IoT devices that collect, analyze, and adapt to building data. These sensors collect information about every part of building operations to help manage and maintain the most optimal building environments. Digital twin technologies are often combined with smart building IoT systems to provide an intuitive 3D model of smart buildings for faculty managers that does not require any technical expertise to navigate.
Smart building IoT drastically increases productivity and sustainability while reducing costs, training time, and downtime. In particular, it makes maintaining security and compliance easy with detailed records and proactive maintenance plans.
6 operational benefits of including IoT and digital twins in smart buildings
Smart building technology can be intimidating due to the specialized knowledge required. Digital twins simplify building management with an intuitive, visual interface. Complex data becomes accessible, allowing you to make faster, more informed decisions that improve efficiency and reduce energy costs.
1. Bridge the skills gap with an intuitive visual interface
Finding experienced staff with the right expertise to implement smart building technology is particularly challenging. Digital twins offer the perfect solution by turning complex control systems into simple, visual interfaces anyone can easily navigate.
Check out how easy it is to navigate 3D virtual space below.
Digital twins provide an interface that’s as engaging as a game. You can even create training simulations for critical operations that can help reduce training time by 50%.
Connor Offut, Cofounder and President at Aetos Imaging provides a vision of the future saying, “The divide between the real world and the digital world will get smaller as what’s known about buildings in virtual space approaches parity with what’s known about them in physical space. It will open up so many opportunities for better city designs, better infrastructure planning, better training, and better thought processes about the built environment as a whole.”
2. Off-site troubleshooting in real-time
When building management systems fail, every minute becomes critical. Digital twins connected to sensors that are capturing environmental data means you have access to historic and current data from any location. Navigating problems and developing solutions is further improved by continuous advancements in artificial intelligence.
Smart buildings help you:
Evaluate problems remotely, improving first-time fix rates before you even send out technicians
Annotate specific devices or areas directly within your 3D model for remote collaboration by all team members
Cut response times by up to 60% and reduce unnecessary site visits
ArchiTwin, a construction documentation company, reduced travel-related site visits by 20-30%.
Chris Christophers, Founder and COO of ArchiTwin, explains, "Technicians can immediately locate anomalies in the 3D model, assess the surrounding environment, and often fix issues without leaving their desk." This remote visibility ensures your problems are addressed before they escalate, protecting your building operations around the clock.
3. Improve safety and guarantee compliance at all times
With connected devices mapped to your digital twin, compliance is streamlined, transparent, and human-error-proof. Automated measurements keep safety clearances accurate, while strong security protects ethernet access and networks—keeping you compliant 24/7.
Upgrading to high-performance 3D technology provides a visual documentation system for your safety-critical infrastructure. In addition to historical data analytics that satisfies insurance companies of compliance, you also can:
Automate compliance checks using integrated IoT sensors
Visualize your safety protocols and emergency systems with clear, accessible representations
Continuously monitor building assets for potential safety risks
Virtually test evacuation routes and emergency procedures for preparedness
4. Data-driven predictive maintenance means you fix things before they break
Predictive maintenance prevents costly (and frustrating) disruptions to operations. For example, Bayer, a global leader in pharmaceuticals and biotechnology, cut project planning costs by 75% with the integration of AWS IoT sensors, and drastically improved maintenance efficiency.
For them, it isn’t just about avoiding breakdowns—it’s about maximizing uptime, extending equipment life by 20%, and providing minimal disruption to building operations. As their team put it, “Having accurate digital documentation integrated with real-time sensor data allows us to detect subtle changes in equipment performance that would be impossible to notice otherwise. We can now predict potential failures weeks in advance, order parts proactively, and schedule maintenance during optimal windows.”
Smart buildings combined with sensors and digital twin interfaces make it possible to:
Visualize building performance data with real equipment and spaces.
Identify patterns that indicate potential failures before your equipment breaks down.
Prioritize maintenance tasks based on actual conditions, not fixed schedules.

The Internet of Things (IoT) has major applications not just for smart buildings, but also smart farming
5. One platform for all your building management and automation
Managing a building’s systems often requires juggling multiple tech tools across different teams, which instantly creates problems because those systems don’t talk to each other. Smart buildings provide an ecosystem that unifies systems into one platform, making management easier and more efficient.
3D interfaces make it easy for you to understand the building as a whole rather than lots of small moving pieces. And collected data and machine learning work together to predict and adapt to current conditions. For example, as occupancy increases in a building and the temperature rises while the air quality declines, a smart building system will automatically adapt, adjusting systems without human input. This centralized approach has been shown to reduce downtime by 25% and increase productivity by up to 75%.
6. Reduce building downtime for 24/hr critical facilities
For 24-hour facilities such as hospitals and data centers, downtime can cost thousands of dollars per minute. Digital twins combined with IoT monitoring create a powerful system for preventing and minimizing operational interruptions. This approach is particularly valuable for your mission-critical facilities where downtime isn't just expensive—it can be dangerous.
Smart buildings help maintain your continuous operations by enabling:
Early warning of potential failures in systems through integrated IoT monitoring
Virtual planning of maintenance activities to minimize operational impact
"What-if" scenario testing before implementing changes to your critical systems
Immediate visibility into your equipment status through layered sensor feeds
Smart building and IoT applications and use cases in practice
Managing modern facilities involves overseeing multiple tools, each generating its own data. IoT brings all data together, giving you real-time visibility and automation—a true all-in-one solution.
Smart buildings adapt to occupancy patterns, biometrics, and user credentials to improve security. Health monitoring shifts from reactive to predictive, allowing for proactive maintenance and less downtime. Automation takes over routine tasks, like adjusting HVAC or lighting based on current usage. Asset tracking ensures equipment and resources are always accounted for, eliminating waste and reducing costs.
Inside a smart building’s centralized control platform
SIMLAB was juggling multiple, disconnected building systems. By integrating Matterport's digital twins with sensors, they created a centralized control platform that unified management and fast-tracked response times. The combination of BIM and real-time sensor data creates a unified approach for easier monitoring, improved collaboration, and faster decision-making.
This central control platform gave SIMLAB the following results:
Unified dashboard: All data is visualized in one interactive 3D model.
Faster response times: Issues are identified and resolved 30% faster.
Remote access: Their team can monitor and manage systems securely from anywhere.
End-to-end visibility: Operational silos were eliminated for a complete view.
Data-driven insights: Optimized overall energy efficiency and system performance.
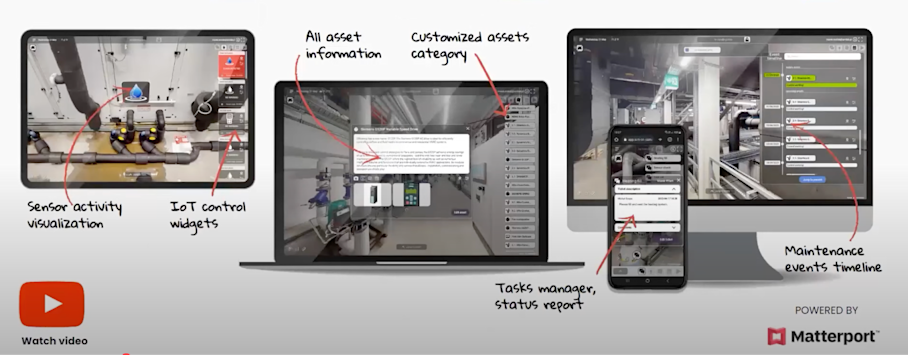
SIMLAB’S control platform contains at a glance. Click here to watch the full video deep-dive.
SIMLAB's CEO Marek Kozlak stated: “Matterport is an absolute game-changer because it brought digitization to the global construction and building management industries. As a result, we’ve created an all-in-one platform that makes building management easier, faster, and more efficient—bringing buildings to life in ways never seen before.”
Security and access control in action
Security systems can flood you with data, but making sense of it is a challenge. IoT-enabled security systems, mapped into your digital twin make staying on top of security easy and streamlined. With 24/7 access and rock-solid network security, your building’s protection becomes more efficient and effective:
Remote control made easy: Manage and monitor your access control points from any location, providing instant visibility without being on-site.
Virtual patrols: Skip the manual walk-throughs and conduct virtual patrols, checking on your facility’s security with just a few clicks.
Intelligent alerts: Receive instant alerts that include spatial context—so you can pinpoint issues like unlocked doors or unauthorized access, instantly knowing the exact location.
Faster incident response: With this spatial awareness, your security team can respond up to 40% faster, ensuring smooth operations and reduced risk.
Smart facility health monitoring
Understanding the overall health of your facility requires monitoring numerous environmental factors. Digital twins make this data visible and actionable in ways traditional dashboards cannot.
Takenaka Corporation, one of Japan's largest construction firms, transformed facility health monitoring in a newly built hotel by integrating environmental sensors with digital twins. This allowed for high-precision remote inspections, ensuring quality control while cutting travel and labor costs.
"Matterport digital twins provide the precision needed for operations staff and enable overseas stakeholders to verify quality remotely," said Yasutomo Matsuoka, Chief Researcher. This AI-driven approach uncovers hidden patterns and anomalies, offering deeper insights beyond traditional monitoring systems.
Automating with IoT technology
Instead of relying on manual inspections and fragmented data, INVISTA’s teams could remotely monitor equipment, identify issues faster, and optimize workflows in real-time. The integration of IoT data within the digital twin allowed for:
Automated system monitoring, reducing the need for manual checks
Cost-effective issue resolution, minimizing downtime and maintenance helps reduce operational costs by an estimated 25%
Optimized energy use, cutting consumption by 15-30% through smarter automation
Seamless integration of HVAC systems, plumbing, and electrical systems for self-regulation
Asset tracking and maintenance scheduling
Managing assets in large buildings can be a logistical nightmare. You need to know exactly where each piece of equipment is, its condition, and when it’s due for maintenance.
Wesbuilt Construction found the solution. By integrating with Matterport’s digital twin, they located assets quickly and easily within the 3D model.
The project tracked plenty of measurable results that deliver serious ROI:
Faster RFI processing: Reduced document errors by 61%.
Improved transparency: Cut rework by 36% with real-time updates.
Reduced project duration: Finished projects 22% faster.
Competitive Growth: Won more projects with 17% fewer claims.
This integration streamlined workflows and collaboration, giving teams remote visibility into project progress.
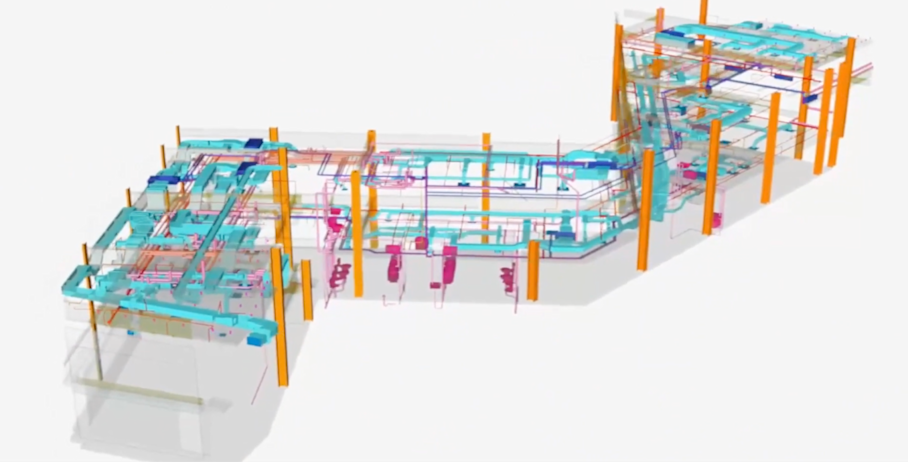
Make smart building management easy with Matterport
Experience enhanced collaboration, streamlined workflows, and improved efficiency—no matter where your team is. By integrating with Matterport’s IoT Digital Twins you can unlock the full potential of your construction projects, and step into the future of facility management. Reach out now to learn how Matterport can help you build smarter, faster, and with fewer disruptions.