How to Build a Resilient Facility Maintenance Plan: Tips, Tools & Templates
Few businesses can afford their commercial property or equipment falling into disrepair for an extended period. If your HVAC has a breakdown on a hot summer day, tenants' customers might be too busy sweating to consider purchases, or staff may have to go home altogether. This type of lost productivity and tenant frustration can severely impact your bottom line — but it’s almost entirely preventable.
That’s where facility maintenance comes in. This important process anticipates the unexpected by taking care of commercial properties, servicing building systems (like that precious HVAC), and maintaining emergency plans and safety measures.
Because of the necessity for facility maintenance, the International Facility Management Association (IFMA) boasts more than 24,000 members, and they buy $526 billion-plus in related products and services. The facilities management industry is projected to have a compound annual growth rate of 5.4% over the next 10 years.
So, how do you create a facility maintenance process? To learn the ins and outs of this important role, below you’ll find a roundup of its many advantages and best practices to help implement your own program.
What is facility maintenance?
Facility maintenance involves the upkeep, repair, and management of a building's systems, equipment, and spaces to ensure safe, efficient, and reliable operations. Maintenance activities include corrective and emergency repairs, predictive maintenance, and regular inspections to maintain optimal conditions for occupants and operations.
For businesses with brick-and-mortar property and equipment, it’s crucial to have behind-the-scenes processes to keep everything running smoothly. That’s what facility maintenance is — managing a commercial building to ensure it’s a safe work environment, that it operates without a hitch, and that it makes it easy for workers to get things done.
A facility manager will also be responsible for general building maintenance (inside and out), servicing permanent fixtures like HVAC systems, and accomplishing all tasks while staying on budget.
While the terms are often used as synonyms, facility maintenance isn’t the same as industrial maintenance or property maintenance. Instead, industrial maintenance specifically applies to manufacturing facilities, while property maintenance is for residential buildings. Facility maintenance typically applies to commercial properties without a manufacturing function.
Are you a manufacturing professional? You might be interested in exploring how digital twins can enhance manufacturing processes and strategies—check out our blog for a deeper dive.
Why properties need facility maintenance
As aforementioned, facility maintenance is crucial to keep a commercial property operating and to maintain safety standards for everyone who occupies the building. This role also supports a laundry list of specific functions, including:
Preventative maintenance for long-term cost effectiveness
Unfortunately, all equipment, systems, and buildings deteriorate over time. However, regular preventative maintenance and assessments can keep your property and capital assets running with minimal downtime.
Just like a car needs regular oil changes and tire rotations to run smoothly, facilities need routine maintenance to ensure smooth operation without major hiccups and expensive repairs. That’s why preventative maintenance tasks and check-ups are a crucial aspect of facility maintenance — regular attention can curb the risk of downtime and extend the life cycle of your property and equipment.
Safety inspections and compliance
Every property has safety best practices to stay compliant with state, federal, and industry standards. Facility maintenance can ensure businesses pass inspections easily and prevent accidents, sickness, or injuries on the property.
That often includes comprehensive fire safety checks for working alarms, sprinklers, and fire exits. Additional checks will also include:
Natural gas safety inspections
Security alarm testing
Annual electrical checks
Checking plumbing and pipes regularly
Ventilation and air quality checks
Ensuring tenants aren’t violating maximum occupancy rules
Preventing other hazards like icy sidewalks in front of the building
Emergency response and preparedness
Part of the role of facility managers is to create, maintain, and execute an emergency preparedness plan for the property and its tenants/residents. The U.S. Department of Homeland Security reports that creating a comprehensive emergency plan can help “manage the entire life cycle of a potential crisis,” including the stages of training, equipping, exercising, evaluating, and taking corrective action.
To prepare for unforeseen circumstances like tornadoes, fires, and other possibilities, facility managers:
Create evacuation routes
Designate meeting spots
Communicate plans to the building’s residents/tenants
Regularly assess emergency plans for necessary updates
Tenant and resident communication
Because so much of facility maintenance happens behind the scenes, tenants and residents often aren’t aware of all this work happening in the background.
However, another duty of facility managers is to communicate critical information to tenants and residents regarding upcoming safety inspections, emergency preparedness drills, or preventative repairs. That way, everyone is aligned on upcoming work or inspections and prepare accordingly.
Budgeting and cost management
Building/equipment maintenance, repairs, safety inspections, and record-keeping all have their own costs — and they can add up quickly. The costs to maintain facilities have skyrocketed in the last few years thanks to rising energy costs, inflation, and labor shortages.
Fortunately, a facility manager can monitor the cost of implementing safety best practices and the upkeep of the property and equipment. They can also double-check when repairs or maintenance fall under a warranty — which can save businesses serious money.
When a facility manager can closely track these activities, it’s far easier to keep a property up and running while staying within a budget.
Record-keeping and documentation
A facility maintenance program means you’ll have a dedicated person to monitor all of the activities outlined above. Up-to-date documentation ensures you can prove compliance with health and safety codes, and keep important equipment safety info and manuals accessible.
Facility managers track and keep records of:
Preventative maintenance and repair schedules (and their recurring work orders)
One-off work orders for repairs, installations, etc.
Emergency preparedness plan
Past and upcoming safety inspections plus proof of compliance
Other routine inspections and assessments
Budgets for all facility maintenance work
5 tips for a resilient facility maintenance plan
Now that you have a good grasp on the many benefits of facility maintenance, it’s time to implement a program of your own. But before creating your own facility maintenance process, review these tips to compile a seamless plan for your property.
Create and upload inspection checklists
With a long list of safety inspections and routine assessments to perform throughout the year, it’s easy to miss checking off a piece of equipment or reviewing a specific area of a property. Fortunately, a little documentation can go a long way to help.
Create thorough checklists for all recurring inspections and assessments. From there, save them in a shared folder so that it’s easy for facility maintenance workers to access and collaborate on these checklists when they need them.
Digitize equipment info, systems manuals, and warranty data
Facility managers have to keep up with mountains of paperwork for equipment and systems (like that HVAC we mentioned). To stay on top of it all, you can centralize and digitize all your systems and equipment details plus warranty data. With a Matterport digital twin, you’ll have an immersive rendering of your property. But this 3D floor plan goes far beyond just capturing the layout and measurements of the interior. With the Matterport platform, facility managers can add Matterport Tags that highlight property features and equipment, document past equipment failures and repairs, and link out to an appliance/system’s warranty and model info.
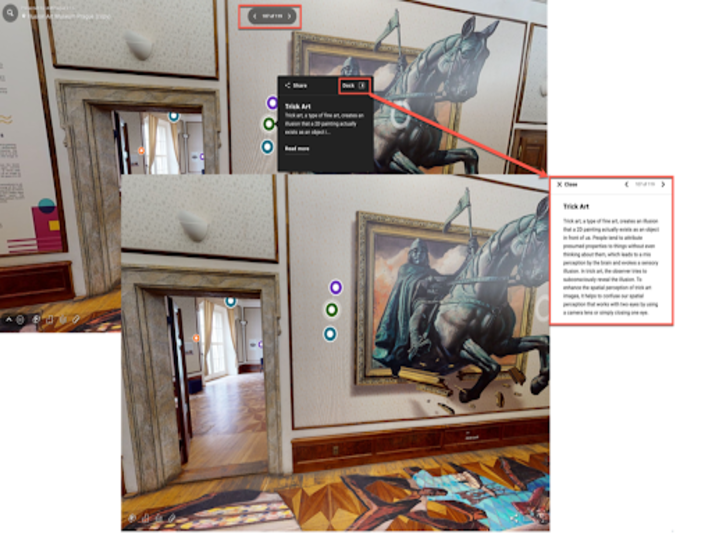
Example of Matterport Tags providing additional info on features in a space.
All this crucial facility data is kept right inside Matterport, where it’s centralized, easy to access, and shareable with team members or vendors.
Create schedules for repairs and installations
To ensure preventative and corrective maintenance aren’t missed, facility managers can create a schedule for these regular appointments.
Use a digital calendar or spreadsheet to document the dates and triggers for routine assessments, safety inspections, preventative repairs/services for equipment, and any other recurring appointments. From there, you can share your virtual calendar with your maintenance team, suppliers/vendors, and any other relevant stakeholders.
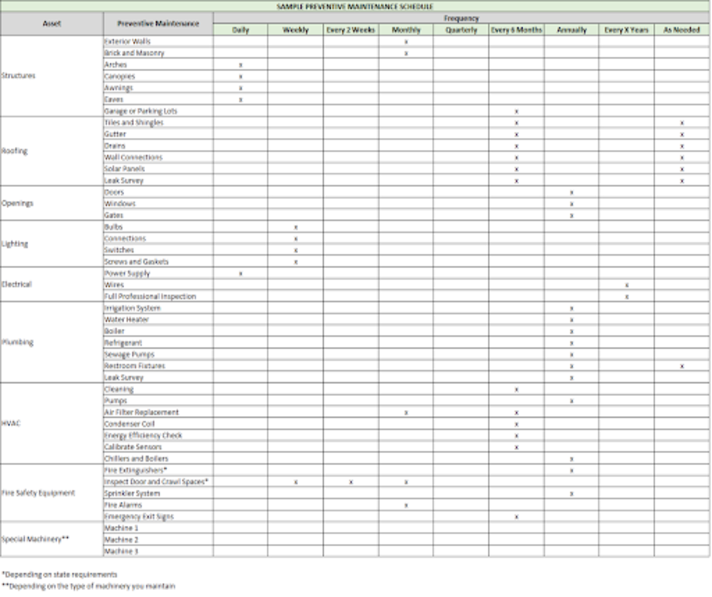
Sample preventative maintenance schedule
Share your building’s digital twin with suppliers and inspectors
For suppliers and vendors doing repairs and maintenance, they’ll need to know where your systems and equipment are located on your property. That’s where a Matterport digital twin and schematic floor plan can help.
Matterport’s schematic floor plans are a cost-effective way to generate professional-grade floor plans for your property. Give your vendors and suppliers an at-a-glance view of your property so they understand the basic layout of the building. That way, they know exactly where to go for installations, repairs, and preventative maintenance.
Quick service and repair appointments mean less hassle for facility managers and suppliers — managers don’t even need to be on-site to instruct vendors where to go.
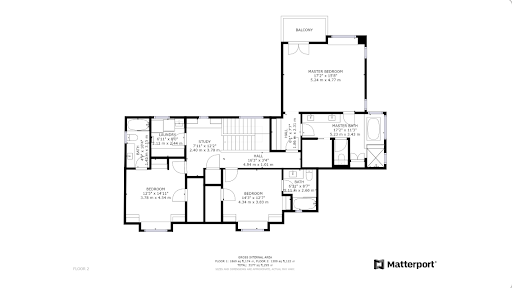
Example of schematic floor plan. Source
Matterport’s digital twins are a comprehensive, virtual version of a property. A digital twin can serve as a 3D walkthrough of your building’s interior space — which makes it ideal for routine assessments and virtual inspections for health and safety codes.
Facility managers can leverage digital twins to inform their emergency preparedness plans. Design evacuation routes and more using the 3D walkthrough of the space.