How to Create a Digital Twin of a Building (+ Tool to Build Accurate Virtual Replicas)
Digital twin technology is finding powerful use cases across industries. In the manufacturing and AEC (architecture, engineering, and construction) sectors, digital twins of buildings give teams a deeper understanding of their physical space across its lifecycle — from initial designs to construction progress, then ongoing use and maintenance.
In this article, we’ll explore how teams can get started creating digital twins — and how a trusted partner like Matterport can simplify the process. With Matterport in their corner, teams across AEC and manufacturing industries are empowered to capture, edit and share photorealistic 3D scans of AEC projects and collaborate using these virtual replicas of their properties.
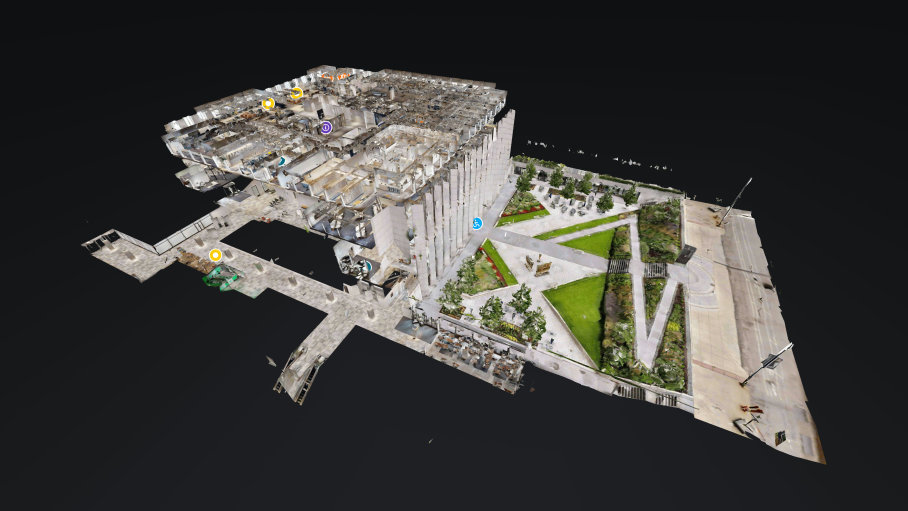
What is a digital twin of a building?
A digital twin of a building is an immersive 3D virtual replica of a physical property. At the most basic step, Matterport digital twins are generated from photos by AI to render dimensionally accurate, navigable virtual models. The term digital twin is very broad though, and can also refer to highly integrated IoT and systems data that offer real-time and even predictive modeling based on the information plumbed into them.
Examples include sensor data like temperature or moisture, RFID data like employee foot traffic and badge entry, and geolocation tracking of vehicles or supplies. Ideally, the two are used in harmony so that the people running businesses and making decisions can see the integrated system information they need, in the context of the physical space it’s measuring to make well-informed and fast decisions.
Digital twin technology has found applications in a variety of industries and use cases. From real estate to facilities management, digital twins in manufacturing and businesses of all shapes and sizes are unlocking the power of virtual 3D models, keeping them informed across the building lifecycle.
But capturing the built environment is particularly useful for AEC and manufacturing teams who want to quickly understand and communicate spatial information, often at factories or job sites across the state or country. Fortunately, platforms like Matterport make it easy to create your initial digital twins.
Benefits of creating a digital twin
The future of smart building, as demonstrated by smart building examples, starts with 3D digital twins. Whether you’re looking to install a new HVAC system or update your building to align with new sustainability standards, digital twins that integrate the visual space with live system data give your team the immersive, photorealistic view needed to improve collaboration and decision-making.
Here are a few benefits that manufacturing and AEC teams will enjoy when they embrace the power of the visual digital twin before system integration is even included.
Streamlined project management: Teams are able to get started with projects faster and complete them on a faster timeline and meet projected milestones with help from a shareable, dimensionally accurate, digitized model of their physical environment.
Reduced site visits: With a 3D digital replica of your building on hand, you won’t need to frequently visit your property to keep up with construction project progress or space planning.
Easier communication with clients or operators: Digital twins promote connectivity between project stakeholders and speed up Manufacturing workforce training and communication. For instance, if you want to show your client the latest milestone in your renovation project, all you have to do is send them a recently created digital twin of the updated property. Industrial operators can access a digital twin on their manufacturing floor tablet for immediate reference about an area.
Increased sustainability: Energy efficiency isn’t just good for the planet — it’s also cost-effective. Digital twins enable property and project tours without the need for travel or commutes.

How to build digital twins in 3 steps
Building a digital twin involves creating a virtual replica of a physical object or system, connected through real-time data streams. It is commonly done in 3 steps:
Define the purpose and scope of the digital twin and gather real-world data from IoT sensors and devices. To do so, choose the appropriate modeling approach and use simulation and analytics to replicate the behavior of the physical entity.
Implement real-time data integration to keep the digital twin synchronized with its counterpart. Create a user interface for visualization and interaction, ensuring security and privacy measures are in place to protect the data.
Continuously improve and update the digital twin as the physical system evolves, and explore integration possibilities with other relevant systems to enhance its capabilities.
Building a digital twin using Matterport
Creating a digital twin might seem like a complicated, time-intensive task. That’s why Matterport is summarizing the whole process, from capture to digitization. Once you’ve picked a capture device (ie, a camera), you can just download the Matterport app, choose a subscription plan, and have a digital twin ready to go within 48 hours of the capture.
Here are the three simple steps to building digital twins in Matterport:
Capture
A variety of digital cameras can capture a digital twin — even the phone in your pocket. If you’re looking to get started quickly, simply download the Matterport app and start capturing. For smoother scanning of your physical space, Matterport Pro Series cameras can bring your indoor and outdoor spaces to life. Or you can work with one of Matterport’s Capture Technicians to scan the space that becomes your digital twin. Spaces larger than a typical residential home are good candidates for hiring a service provider, as high-quality DIY or phone capture can be time intensive.
Edit and document
Once you’ve captured your space and the digital twin is rendered within 48 hours, you can annotate it as you see fit. This might include adding measurements, tags, or notes that will be useful down the road. And Matterport integrates with existing software to help you get the most out of your digital twin. For instance, architecture teams can quickly purchase BIM files or digital floor plans to streamline modeling and drawing time.
Share and collaborate
Matterport makes it easy to share your digital twin with other people on your team, clients, or even the entire employee base of a company, making collaboration simple. Matterport’s digital twins can also be added to your real estate or retail website easily, helping you connect with customers and improve their experience.
For detailed information on building digital twins with Matterport, check out the Matterport Help Center.
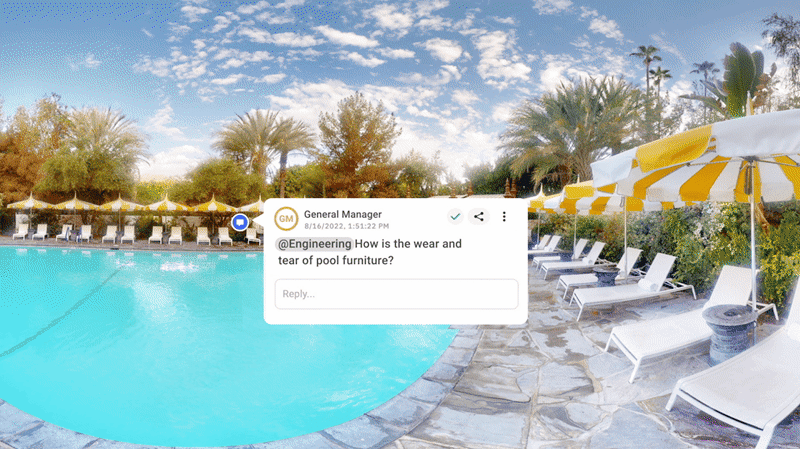
Building a digital twin FAQs
What is a digital twin’s role in BIM?
Digital twins can expedite the creation of BIM files. AEC teams use BIM to plan and analyze a building project. Then, once the building is complete, the building owners might use digital twins and the BIM file to inform building operations.
Is a digital twin a 3D model?
If you’ve heard the phrase, “all squares are rectangles, but not all rectangles are squares,” Matterport digital twins are immersive, 3D models of physical assets, however describing a digital twin as a 3D model sells short its full potential functionality. Digital twins that are integrated with live data, machine learning technology, artificial intelligence, and predictive modeling can help teams in AEC and manufacturing work smarter and faster—especially when used for predictive maintenance and performance optimization.
Which companies use digital twins?
Businesses across industries are using digital twins to improve decision-making, strengthen collaboration, and streamline project timelines. From real estate to smart cities, learn more about the teams using digital twins to power a digital transformation in their organizations.