Guide to Digital Transformation in Manufacturing [2024]
Benefits & Inspiration To Get Started
Manufacturers are looking for new ways to be more efficient, safe, and grow. And while the manufacturing industry trends are more traditional, this sector’s digital transformation moment is so big it has its own name, Industry 4.0.
According to one estimate, the market size for digital transformation in manufacturing is $307.87 billion as of 2023. More and more manufacturers are making the upfront investment in high-tech tools that’ll help them modernize and move into Industry 4.0.
But deploying digital transformation processes in manufacturing can feel like peeling an onion, without any distinct end in the continuous cycle. That’s where we can help. Learn more about the competitive advantages, how some manufacturers have incorporated technology to innovate, and a few handy tips to enhance your decision-making about where to tackle new digitized capabilities in your own manufacturing operations.
What is digital transformation in manufacturing?
Digital transformation in manufacturing involves integrating new technologies, such as digital twins, IoT sensors, and artificial intelligence (AI) to monitor and automate manufacturing operations.
This kind of digital transformation accelerates insights and can span an entire facility and address everything from day-to-day manufacturing processes to supply chain management.
3 key benefits of digital transformation in manufacturing
As mentioned above, digital transformation in manufacturing provides an opportunity to address operational challenges and inefficient processes. This transformation, and the move to Industry 4.0, can help manufacturers become more efficient in multiple ways across their entire operations.
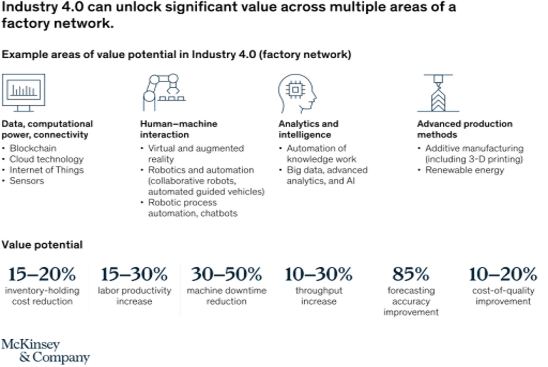
The digitization in the manufacturing sector boasts a wealth of other benefits, such as:
Improved production efficiency and sustainability
A more resilient supply chain and inventory transparency
Let’s take a closer look at how.
1. Improved production process efficiency
When your manufacturing company can increase both the quality and volume of product output, it’s a huge boon to your bottom line. And digital transformation in the manufacturing industry can achieve just that.
Thanks to digital twin technologies that translate the physical world into an accessible virtual version, manufacturers can access and process the data they need to understand the state of operations from facility maintenance, to inventory management, to daily operations and training. Having this level of visibility helps to get ahead of downtime that might have been a result of existing inefficiencies.
2. More resilient supply chain and inventory transparency
Many manufacturers often run into unforeseeable supply chain disruptions which serve as the impetus to reassess their supply chain management. Leveling up existing processes by using digital transformation is a great way to address that.
Supporting the optimization of operations, digital twins make supply chain more resilient and improve inventory management. For example, AI and predictive analytics help manufacturers more accurately forecast demand and even play out different scenarios (economic conditions, world events, etc.) to see how they impact demand and plan accordingly.
3. Lower operational costs
The promise of higher productivity plus a more agile supply chain doesn’t have you convinced? Perhaps the potential cost-savings will turn your head.
Higher production volume and quality due to digital transformation offer a sizable bump to manufacturers’ bottom line. One report showed that good digital tools can boost productivity which leads to cost-savings upward of 5%. Compare that to more orthodox methods of cutting costs (think layoffs, cutting production corners, etc.), which only offer about 2% in savings.
Next, let’s touch on the cost of maintaining your equipment. Preventative and predictive maintenance for your digital manufacturing equipment is a must to avoid downtime and to increase the lifespan of your machinery. But it’s easy to put these kinds of regular repairs on the back burner in favor of more urgent needs.
But with a little help from digital twins and smart sensors, anticipating maintenance and coordinating repairs can be drastically improved.
5 ways Siemens used digital twins to innovate their operations
Siemens, a global manufacturing and technology leader, enhanced its operations and customer experience through the use of Matterport digital twin technology. We will cover the different ways in which Siemens is using the flexibility of Matterport digital twins to improve manufacturing business processes and level up from traditional manufacturing.
1. Enabling remote discussions about manufacturing operations
In Asia, Siemens captured around 4,000 m² of a manufacturing plant as a digital twin, encompassing the shop floor and warehouse, and produced a digital twin. This enabled remote discussions between internal stakeholders and customers that showcased the plant’s manufacturing capabilities in an immersive, explorable way, similar to being on the plant floor. The added benefit was the fact that these discussions could take place in a format that did not interrupt business-as-usual operations with external visitors and demos.
2. Corporate campus digitalization for training
Siemens digitized 9 buildings and 1 Experience Center in their corporate campus in Alfragide, near Lisbon. Overall, nearly 30,000 m² of Siemens facilities have been digitized. The digital twins became particularly popular during the pandemic and functions now as an important tool for accessible training and virtual tours.
3. Integration with IIOT (Industrial Internet of Things)
At the Siemens Experience Center in Alfragide, Portugal, digital twin technology is showcased in conjunction with IoT sensors. This integration between digital twins and Industrial IoT sensors provides clear, contextual insights into environmental factors that enhance remote monitoring and enable data-driven spatial planning decisions, showcasing an example of real-world applications of industrial internet of things (IIoT) in action. This is a significant improvement from static dashboards.
4. Facility relocation and spatial planning
Siemens also used Matterport digital twins for a factory relocation in Berlin. The technology allowed for the virtual staging of equipment, confirming spatial fit with high accuracy, and facilitated collaborative planning without the need for physical presence, saving time, cost, and effort.
5. Virtual trade shows and product showcases
Apart from applications related to manufacturing operations, Siemens found a marketing use case for digital twins. Siemens Energy developed a virtual tour of an E-House (a prefabricated substation) using Matterport. This provided an immersive experience for potential customers, showcasing the new product in detail remotely and bolstering sales and marketing efforts, while reducing travel and logistics costs.
To learn more about how Siemens uses Matterport to keep innovating, check out the Siemens case study. As evidenced by Siemens, digital twins are very flexible in their application and can support a breadth of business functions.
How to adapt to the future of digital transformation in manufacturing
Now that you’re ready to move forward with a manufacturing digital transformation journey of your own, you’ll need to ensure you set yourself up for success. Here are a few additional tips that can help you implement the right tools to improve your manufacturing process.
Look for tools that offer multiple benefits
While niche tools that offer a singular purpose are great, consider tools that provide more than one advantage. For example, a Matterport digital twin integrated with AWS Twin Maker makes it easier to experiment with a new production line without risk as well as tracking equipment maintenance and repair.
Centralize your equipment and operations monitoring
Choose tools that allow you to remotely monitor your business operations from one, central hub. That way, you can keep a finger on the pulse of your facility’s health without being chained to your desk.
Make employee training and onboarding easier
Speed up employee education with immersive and interactive learning experiences, like those provided with augmented reality (AR) and digital twins. That way, you can easily exchange knowledge and boost employee health and safety through remote training.