How to Monitor Construction Work Progress: A Modern Approach
Construction Progress Monitoring and Digital Twins: The Perfect Pair
Any seasoned professional in the construction industry knows, that when it comes to construction projects, delays can pile up faster than rubble after a demo. Construction progress monitoring is key to ensuring projects are completed in a timely manner. But, in the past, construction progress monitoring itself was a time-consuming chore.
Before modern tech, construction progress monitoring entailed on-site visits, multiple building drafts, and more. And, it left tons of opportunities for people to make costly mistakes. Yet, forgoing this process entirely can lead to project bloat, delays, and, ultimately failing to deliver for a client.
Fortunately, today’s technology allows for an unprecedented level of collaboration with construction progress monitoring. Not only this, it also makes the process as a whole less time-consuming and easier than ever. But first, why do you need to worry about construction progress tracking at all?
The significance of construction progress monitoring
Construction progress monitoring is just as it sounds — the act of monitoring how a construction project is coming along. This is important throughout all the construction phases for a number of reasons.
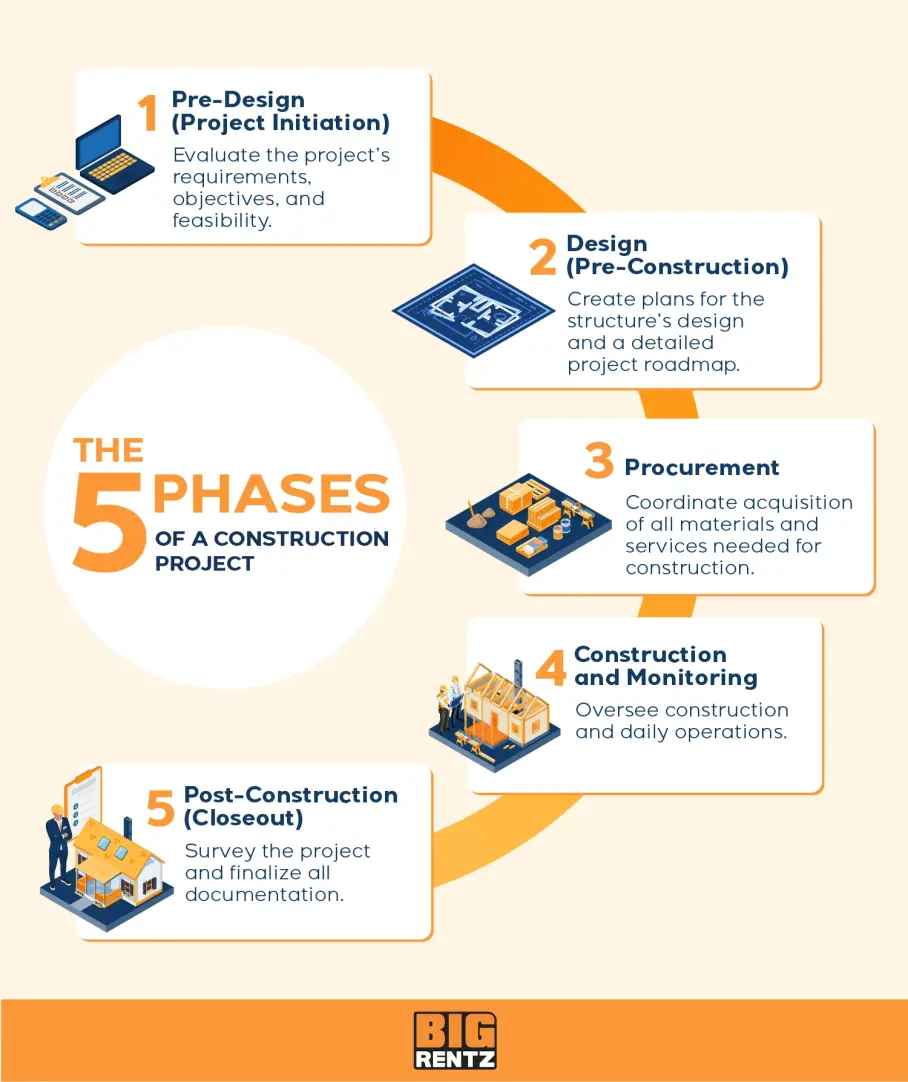
Tracking project timelines and deadlines
Construction projects can be anywhere from a few months to multiple years in length. Whether you’re dealing with a short project or a long one, delays can happen for any number of reasons:
Unexpected material or labor shortage
Challenges with weather
Communication issues
Lack of planning
Design issues
Safety incidents
Changes of scope
The list goes on and on. No matter the reason, the end result is the same: delays and missing your deadline.
When you’re tracking progress throughout the construction process, you’re able to stay on top of these various challenges and keep the client and your deadline realistic. For example, if you’re routinely tracking the construction project, you’ll be more likely to notice a material shortage coming. This would allow you to find an alternative solution before actually running out.
Budget control and cost management
Simply put: accurate construction progress monitoring allows you to better stay on top of spend. When you’re routinely checking in with your team and the project itself, you’re more likely to notice if labor is running over, unexpected challenges have bloated costs, and so on.
Quality assurance and compliance
Planning and design are crucial to successful quality assurance and compliance with any regulations. While you likely addressed these things during the planning and design phases, things don’t always go as planned during construction.
Part of routine construction progress monitoring is checking that as-built documentation aligns with as-designed. By doing this, you’re more likely to catch any quality control or compliance issues before they turn into a bigger problem. (And, this saves time and money, going back to the previous point about cost.)

Risk mitigation
Similar to quality assurance and compliance, frequent project monitoring makes it more likely that you’ll catch any safety or risks early on.
For example, if you’re not practicing progress monitoring, you might not notice that a substitute material used for a wall (due to a shortage) isn’t going to safely hold up to the stress of the building when completed. Whereas, if you were running regular project checks, you’d catch this early on.
Resource optimization
Technology is a key part of a modern construction progress monitoring strategy. With modern tools, you can get real-time data and real-time progress reports. With this information, you can easily check project progress for various parts of the build, and then allocate resources where it makes the most sense. This can help you drive down labor costs, reduce bloat, and even finish a project quicker.
4 key phases involved in monitoring construction progress (with best practices)
Depending on who you ask, there can be several steps to construction progress monitoring. To keep things simple, we’ve broken it down and provided four phases for monitoring construction progress.
Phase 1: Define the construction project schedule
The first and arguably most important step of proper construction progress monitoring is defining your project schedule. Whether you’re working with a client or handling in-house work, this step largely sets the pace for everything that follows.
Work with key stakeholders and figure out:
The scope of the build or renovation
Labor required
Potential risks and complications like permitting
Materials needed
Zoning and building codes for the area
Etc.
Best practice: It’s best to underpromise and overdeliver. Don’t oversell yourself and bite off more than you can chew. Instead, set a realistic, clear timeline that leaves little to the imagination. Factor in potential delays when doing this. Best case, you deliver early. Worst case, you might land right on the promised time.
Phase 2: Establish project goals and milestones
While this is the second phase, you can incorporate elements of this in the first phase. Here, you want to focus on establishing goals and milestones. Most of these milestones will relate to the actual construction, but you also want to mix in some that are focused on pre-construction and client or stakeholder approval.
Best practice: Make your goals and milestones clear and measurable. For instance, “complete tasks faster than the last project” isn’t very concrete, nor does it give you a number to aim for. Instead, set a goal like “complete design phase in under five months.”
By having clear and measurable goals and milestones, you have a guiding north star to follow during your progress monitoring. These goals and milestones can keep you in check as you monitor progress, and make sure you’re always taking steps to reach them faster.
Phase 3: Communicate progress with stakeholders regularly
Clear communication between you, your team at the construction site, and any stakeholders is crucial to smooth sailing and making sure the unexpected is always clear. As you monitor construction progress, make sure you’re always keeping essential people in the loop.
This is also where milestones are important, as they give you a frame of reference when communicating progress to stakeholders.
Best practice: Implement technology to create a single source of truth for collaborators. This is where something like a digital twin platform can come in handy. For example, without digital twins, you’d have to send clients or stakeholders numerous files, pictures, and communications to convey progress. With Matterport digital twins, you can send secure invites to stakeholders and have everyone collaborate on a single, 3D, visual source of truth — no matter where they’re located.
From there, you can comment on the digital twin, take measurements, leave notes, and keep stakeholders in the loop as if they were right there on the site.
Phase 4: Identify delays and issues
Despite being the last phase, this is an ongoing phase that should run throughout the entirety of your construction progress monitoring.
During your monitoring processes, you should be checking materials, labor use, and so on. At any of these points, if you notice material shortages, permitting delays, issues with labor, unexpected weather on the horizon, etc., take note and flag it.
Again, this is why routine progress monitoring is crucial to staying on track. When you’re frequently checking things, you’re more likely to notice these delays and issues, and more likely to get ahead of them.
Best practice: Build some buffer in the plan to account for course correction before you give an updated timeline to your stakeholders. Again, underpromise and overdeliver.
4 ways digital twins bring clarity to construction progress monitoring
Digital twins are revolutionizing the construction process as a whole, and this includes progress monitoring.
Digital twins, especially those provided by Matterport, can be created in far less time and much more affordably than survey-grade scans. For example, with 360 cameras, a space can be captured in as little as 30 seconds. This allows you to have scans completed each day, which enables near-real-time digital twins. A next step up in camera with a Matterport Pro2 or Pro3 offers massive jumps in dimensional accuracy and image fidelity. So much so that those digital twins can be exported as LOD 200 BIM files and CAD files, which come in handy during pre-construction phases.
But, the benefits of digital twins in construction progress monitoring don’t end there (especially when you integrate digital twins with BIM). Let’s dig a bit deeper into some of the biggest advantages.
1. Improved collaboration
Matterport digital twins can be quickly created and easily shared. This allows you to make them every day, not only at major milestones. From there, you can share them online with both internal and external stakeholders.
Using Matterport Notes, you can leave comments on digital twins, asking about various changes or calling attention to areas of concern. This enables quick and effective collaboration, whether stakeholders are under the same roof or spread around the globe. And, the only person who has to be on-site is the one scanning.
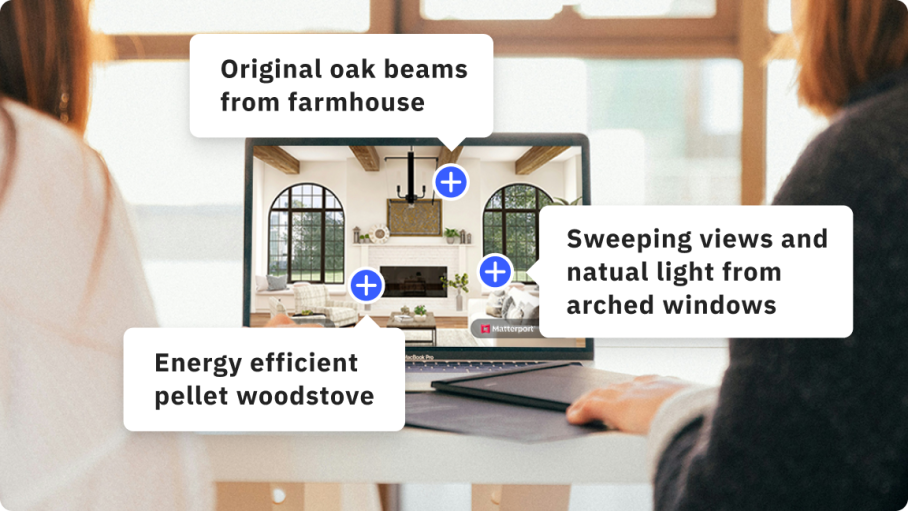
Bulley & Andrews, a construction firm helping a major retailer in Chicago. The retailer was headquartered in Florida, but their new location was in Chicago. The budget only covered flying stakeholders out to Chicago once or twice. Bulley & Andrews had a better idea.
After consulting with VIATechnik, Bulley & Andrews went with the Matterport Pro2 3D Camera. This enabled them to supply immersive walk-throughs of the retail location throughout the project, keeping the client in the loop the entire time. And, without anyone having to fly back and forth. Not only did this reduce travel time, it also helped them with quick decision-making, despite distance differences.
2. Accurate documentation
Having accurate documentation is crucial to construction progress monitoring. Without it, your reports are inaccurate, the info you give stakeholders is inaccurate, and countless issues loom just overhead.
Digital twin technology makes it possible to go beyond manual measurements and streamline documentation as a whole. With Matterport cameras, you can quickly scan spaces and generate high-density point clouds and digital twins. From there, you can view comprehensive, auto-generated measurements of the space and measure the dimensions of things within it, or even export the space as a detailed floor plan. All of this makes it possible to not only have accurate measurements and documents, but enhance record keeping as a whole.
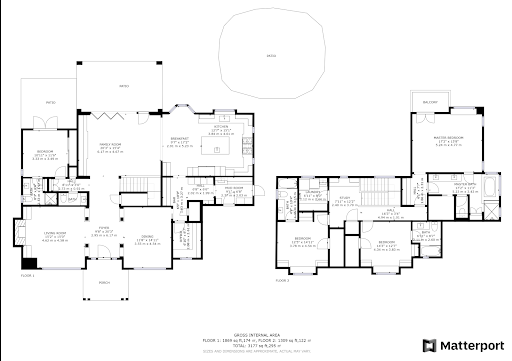
Knutson Construction, based in Minnesota and Iowa, works with world-renowned healthcare providers and universities. As a family-owned construction company, they strive to deliver excellent service and stay up with the curve. Construction often lags behind in tech, but they didn't want to be a part of this problem. So, they turned to Matterport.
Using Matterport 3D scans, the team at Knutson has been able to produce accurate construction documentation twice as fast as they used to. They no longer measure spaces by hand at the job site, and instead get fast imagery and dimensions straight from their scans. The ease of use means more folks on site can grab a camera and start scanning versus waiting for a VDC Manager’s availability. Now, one person can efficiently do what previously took four: estimator, pre-construction manager, project manager, and virtual design construction manager.
3. Simplified feedback process
Feedback is another core element of successful progress monitoring. When your project team is able to quickly get feedback on construction work from the site, they can react in kind. Similarly, when team members on the site are having issues, say, with a specialty contractor or another supply chain element, they need a way to send this feedback to your leadership.
Digital twins can simplify this communication, translating into a more effective monitoring process.
Your team and stakeholders can access Matterport digital twin files from virtually anywhere. Then, they can leave notes and comments, pointing out any areas of concern or noting reasons for change. This makes it easier for you to monitor the project, or even multiple projects, as well. And, you end up with a historical document that you can learn from, resulting in smoother future projects.
The Damen Shipyards Group works on high value projects, where strategy and coordination can mean the difference between smooth sailing or disaster. Damen's clientele varies, with some visiting the shipyard twice to check on a build, and others staying nearby and checking in frequently. Because of this, an efficient feedback loop is essential.

Damen Shipyards Group partnered with Matterport during the COVID-19 pandemic to give customers an inside look when in-person visits weren't possible. The solution stuck. Now, the Damen Shipyards Group uses Matterport as part of their regular workflows for a number of reasons. One of the biggest benefits? Customers and engineers can all offer feedback on digital twin files at any time, allowing collaboration across the country.
4. Improved handover documentation for maintenance and risk management
Construction progress documentation can be invaluable in project completion and handover documents. Digital twin technology can bolster the assets that keep clients coming back time after time.
You can use digital twin 3D models as records for maintenance. Northfield Public Schools acts as a great example. They partnered with Knutson Construction to build a new facility. In the midst of the COVID-19 pandemic, they still managed to collaborate and build the facility. During the process, Knutson used Matterport Pro2 cameras to continuously capture the project's progress, which they communicated to Northfield stakeholders.
Now, Northfield has detailed digital twin files they can use for maintenance and future renovations. Instead of guessing where wires or pipes are located, they can look at the scans and see exactly where utilities run. This will save them precious time and resources and ensure maintenance is a smoother process for years to come.