Real-World Examples of How Digital Twins Streamline Asset Management
Effective asset management can see a facility running smoothly, safely, and efficiently. But, this is easier said than done. Whether you’re managing ten facilities or one, a sound asset management approach is critical. That’s where digital twins come in.
As a facility manager, you’re constantly juggling numerous tasks, tracking valuable equipment, and dealing with people management. All of this makes it difficult to have “eyes on the ground.” But digital twins provide a real-time, virtual view of your facility, making it easier to stay on top of maintenance, operations, and asset performance, even when you can’t be everywhere at once.
Let’s explore where this technology is headed—then dive into real-world examples showing how it delivers results.
What is a digital twin in asset management?
A digital twin is a 3D, interactive model of your facility complete with assets like HVAC, plumbing, electrical, and safety systems, along with their location, condition, and history. In more advanced cases, it also includes real-time data from connected systems to monitor performance remotely.
For asset managers, digital twins pull together data you already have, like floor plans, inspection reports, and service records, into one visual platform. This means faster access to critical information, better coordination across teams, and fewer site visits without needing to dig through folders or jump between tools.
The future of digital twins in asset management
Digital twins are immersive 3D replicas of physical spaces—built not from models, but from photographic and geospatial data. That accuracy makes them incredibly valuable during construction and for ongoing facility management.
This growing reliance on accuracy is reflected in the market’s rapid expansion:
The digital twin market is valued at $17.73 billion in 2024, with projections reaching $259.32 billion by 2032.
By 2027, 35% of G2000 companies are expected to use digital twins for supply chain orchestration.
Digital twins are rapidly being adopted to help asset managers meet rising standards for compliance and operational efficiency.
With only 10.4% of facility management teams having implemented AI in 2024—but 59.1% expressing interest—there’s significant growth potential as smart building tech and IoT investments accelerate alongside the maturation of AI tools.
How digital twins improve asset management
Managing a facility means keeping tabs on a lot of moving parts—and digital twins make that way easier. Instead of relying on static plans or outdated spreadsheets, a digital twin gives you a living, breathing version of your building or site. It’s built from real images and data, so what you see is exactly what’s there.
Enabled predictive maintenance
Start predicting failures before they happen. By combining IoT sensor data with 3D digital twins, you move from reactive to predictive maintenance—minimizing downtime, cutting costs, and optimizing operations.
How digital twins inform your facility maintenance plans:
IoT connectivity links your devices (motors, HVACs, pumps, etc.) to the cloud via real-time sensors and shows you an accurate virtual representation of current operations.
Machine learning algorithms continuously analyze sensor data to spot performance anomalies like:
Abnormal vibration patterns
Temperature spikes
Unexpected power consumption
For example, using the Matterport and AWS TwinMaker integration, you can recreate an entire assembly line in virtual space to quickly interpret and troubleshoot. Check out how it works in this video:
Reduced downtime
When you avoid catastrophic failure, you avoid extended outages and expensive equipment replacements.
Much like how digital twins prevent maintenance issues, they also reduce downtime by sending alerts on abnormal metrics like temperature, pressure, or RPMs, helping teams act before a full breakdown occurs.
With true-to-life 3D captures, you can get a clear, immersive view of the space. Remote experts have access to annotated key equipment directly inside the twin, guiding on-site technicians with precision.
This kind of visual instruction helps teams troubleshoot faster, especially when working with complex systems. Instead of relying on unclear directions, service techs are pointed straight to the issue.
Optimized performance
Facility managers strive to get peak output from every piece of equipment, but physically checking each station isn’t always practical or possible.
Digital twins combined with IoT connectivity let you monitor asset and workflow performance. This visibility helps you spot underperforming assets, identify bottlenecks, and uncover areas prone to frequent repairs.
Performance optimization doesn’t need to be overengineered. A typical process could include:
Scan space and assets with the Matterport Pro2 camera or Matterport for Mobile
Label and tag relevant assets in your digital twin
Share the twin across departments
Collaborate to identify and fix workflow bottlenecks
In production environments, digital twins become invaluable tools for simulating and refining workflows. This lets you experiment with different setups and implement changes backed by solid data, reducing trial-and-error downtime.
Improved sustainability efforts
Digital twins provide a complete picture of energy use, from individual machines to entire buildings.
This precision can easily help you save thousands on energy wastage. For example, you can:
Reveal poorly insulated zones or equipment generating excessive heat and requiring cooling or heating
Rely on voltage sensors to monitor inefficient machines drawing excessive energy and increasing your carbon emissions.
Access accurate virtual spatial data remotely to cut down on travel emissions.
By focusing on inefficient equipment, you’re able to replace problematic devices and reduce energy use. This not only helps with sustainability, but also allows you to reap long-term savings on energy costs.
Enhanced decision making
Extracting insights from real-time data is everything when it comes to strategic decision-making. Here’s how it works with a digital twin:
Instantly visualize asset performance in context: understand how surroundings affect efficiency and failure points.
Collaborate effortlessly with stakeholders using shared annotations, measurements, and comments on the 3D model.
Leverage cloud-powered analytics to handle vast sensor data without slowing down your local systems
Reference historical data to track trends and compare ‘before and after’ scenarios post-changes
Now everyone from maintenance to the C-suite can collaborate on one central platform.
Improved asset lifecycle management
Facility management is finally getting ahead of wear and tear with digital twins. When everything is trackable and includes historic data, lifecycle management becomes straightforward.
Digital twins improve lifecycle management of your assets in several ways:
See what’s where and what’s due (without site visits)
Spot misuse or suboptimal placement that could wear assets faster
Create smarter schedules for upkeep, not just urgent fixes
For example, using Matterport’s field tag feature, you can tag equipment with all the details that matter: model numbers, serial codes, install dates, and maintenance history. Your team has a crystal-clear, 3D visual inventory system. Check out how it works in this video:
Energy utilities using digital twins for infrastructure like substations have cut maintenance costs and shown energy savings of up to 30%. A hydropower plant study saw a 15% drop in maintenance costs and boosted asset lifespan by 10% after implementing digital twins.
Employee training
Much like how a Formula 1 driver uses a simulator to practice racing lines and react to unpredictable conditions, your team can use a digital twin to safely learn complex operations and safety protocols—before ever touching equipment.
Take, for example, a high-powered industrial press that’s both essential to daily operations and risky for new employees to handle. Traditional training would mean shutting it down, pulling in senior staff for supervision, and exposing new hires to potential danger. That’s lost productivity and increased risk.
With a digital twin of that press, new employees can walk through every step of its operation virtually—seeing how it works, what can go wrong, and how to respond—all in a realistic, interactive environment. No shutdowns. No safety hazards. Just better training, faster onboarding, and fewer mistakes on the floor.
In 2025, an estimated 75% of Fortune 500 companies have adopted VR training, marking a major evolution in how businesses train, upskill, and evaluate their employees. Notably, they report a 30% reduction in workplace accidents.
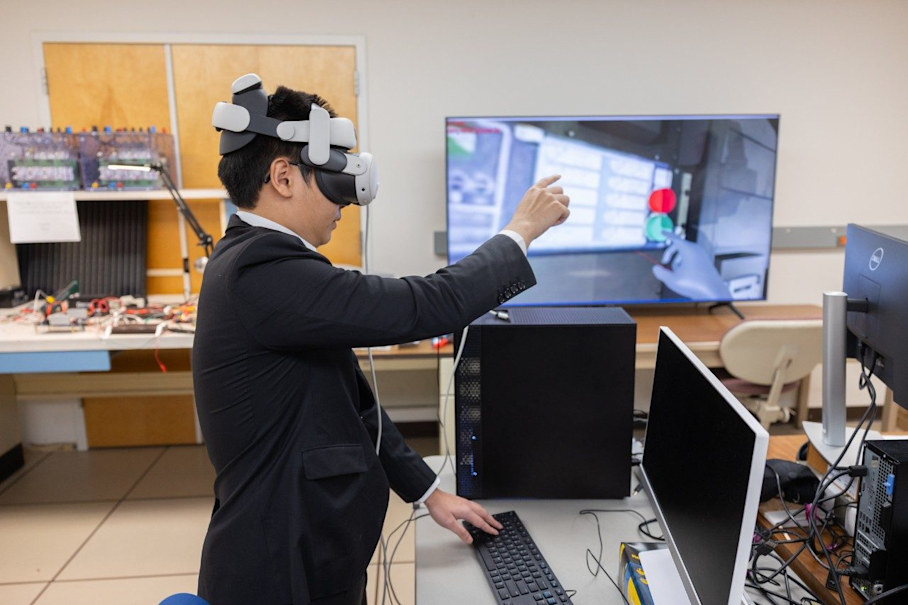
Student Nguyen Khoa Nguyen wears a virtual reality headset while demonstrating the virtual reality training system at a recent Power and Energy Conference. Photo by Ben Murphy for Virginia Tech.
4 practical examples of digital twins in asset management
Digital twins are transforming asset management,—they’re used as practical tools across industries to improve efficiency, reduce downtime, and inform smarter decisions.
Here are four real-world examples of how digital twins are transforming asset management across industries.
1. Northumbrian Water improved the efficiency of legacy asset management
Managing aging infrastructure is no easy task—especially when site access is limited and efficiency is critical. Northumbrian Water, a utility provider in the United Kingdom, faced this challenge across a wide network of wastewater assets. These assets are critical to their processes and the delivery of water.
Using Matterport Pro2 cameras, Northumbrian was able to capture rich images of existing structures and assets and turn them into digital twins. From there, they could integrate scans into Maximo using Matterport 3D Showcase SDK. This allowed them to have "site visits" even at the peak of the COVID-19 pandemic.
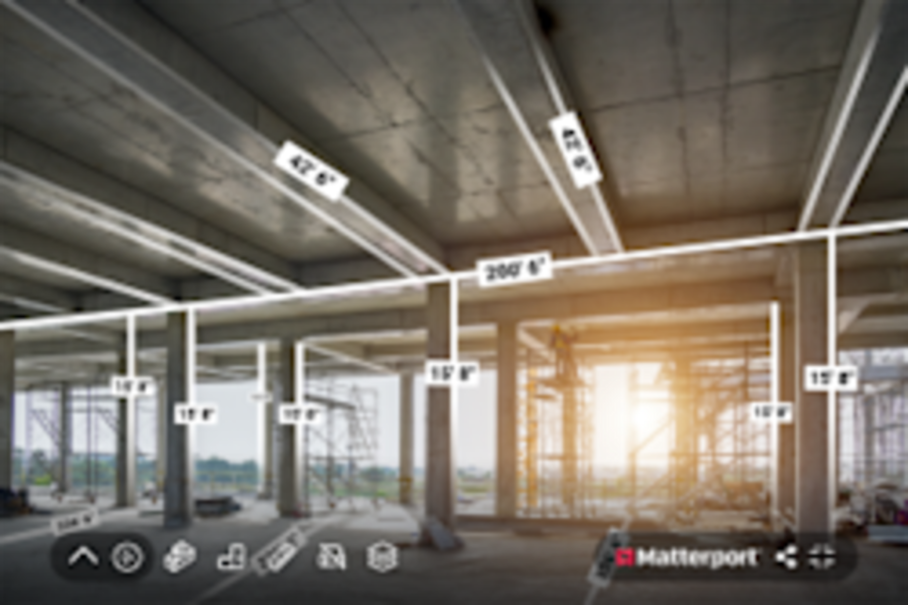
Today, they're able to accelerate initial project startup phases, manage legacy assets, and reduce site visits using digital twins.
2. JFC & Associates increased ROI by enhancing asset uptimes and lifetimes
JFC & Associates specializes in helping companies get the most out of their physical assets and any related operational activities. But, as the company scaled, they knew something had to be done to still deliver the service they were known for.
Using Matterport, JFC is able to deliver digital twins to their clients, enabling them to easily tap on a digital twin for any piece of equipment and access detailed information, and even initiate workflows.
JFC is even able to help with OSHA and safety-related matters using digital twins and sensors. Clients can map out exits, create fire routes, and train employees for the worst.
Matterport API and SDK partner tools are more cost-effective than many competing, more complicated tools. This has allowed JFC to realize better ROI and get new hires up to speed quicker as well.
3. Glass Aftercare transformed client communication and accelerated projects
Glass Aftercare, a leading commercial glazing maintenance company in the UK, has embraced Matterport’s digital twin technology to redefine the way they manage projects and communicate with clients.
By creating immersive 3D digital replicas of client sites, Glass Aftercare eliminated the need for repeated site visits and back-and-forth communication. Instead, stakeholders can walk through a project virtually. This not only improved transparency and accelerated decision-making, but also empowered clients to understand the scope of work visually and in real time.
The result is faster project turnaround, fewer miscommunications, and a complete visual record of every stage of a project.
Glass Aftercare’s business development specialist, Rod Milicevic, explains how they use digital twins in detail in this webinar.
4. CRB helped combat COVID-19 using digital twins
CRB is an engineering, architecture, construction, and consulting firm focused on sustainability. They largely serve biotech and pharma, two industries where efficiency and accuracy are critical.
During the height of the COVID-19 pandemic, one of CRB's clients was involved with Operation Warp Speed. To help them get up and running as quickly and safely as possible, CRB implemented Matterport to capture spaces and create accurate digital twins. Instead of sending six to 10 engineers to the site, a process that took several days, they only needed one person to capture the space.
Chris Link, a regional Virtual Design and Construction Manager at CRB, explains: “In looking for a 3D platform, we prioritized accuracy, ease of use, remote functionality, and flexibility.” He adds, “Matterport is an ideal partner for technically complex and time-sensitive projects.”
Now, post-pandemic, CRB is able to replicate this process with other clients. Their use of Matterport digital twins allows them to work remotely and collaborate, provide virtual tours to customers, and expedite project planning.
Ready to supercharge your asset management strategy?
By transforming buildings and infrastructure into immersive, data-rich digital twins, Matterport helps organizations streamline operations, reduce costs, and make more confident decisions, faster.
Whether you're just exploring digital twin technology or ready to scale, Matterport’s end-to-end 3D solutions offer a smarter, more efficient path to asset management. From capture to collaboration, our platform simplifies the complexity, giving you the insights you need to stay ahead.
Connect with our team to discover how digital twins can integrate into your business.