Scan-to-BIM Process: 7 Steps To Improve Your Workflow [+Example]
The scan-to-BIM process is a transformative step in accelerating the digital evolution of the architecture, engineering, and construction (AEC) industries. As highlighted in recent research, companies adopting advanced digital workflows, including BIM, report significant improvements in project outcomes, including up to 85% enhanced design quality and reduced rework.
Scan-to-BIM bridges the gap between physical spaces and digital models, enabling seamless collaboration, data-driven decision-making, and long-term operational efficiency. By combining reality capture tools with BIM workflows, professionals can achieve higher accuracy, improved collaboration, and enhanced efficiency.
Scan-to-BIM workflow in 7 steps
This guide outlines 7 essential steps to ensure a successful scan-to-BIM process, complete with actionable best practices for each phase.
1. Planning and site preparation
Planning is critical to ensure a seamless scan-to-BIM workflow. This process is transformative for professionals in the AEC industry, such as surveyors and architects, because it ensures accurate, comprehensive data capture that minimizes costly errors and streamlines downstream workflows. Proper site preparation not only improves data capture but also reduces post-processing time, setting the foundation for a successful project.
Best Practices:
Evaluate environmental factors, such as lighting conditions and obstructions, to ensure optimal scan quality. Matterport’s Pro3 Camera, optimized for complex environments, is ideal for accurate and efficient scans.
Create a systematic scanning plan to cover all areas comprehensively and eliminate blind spots.
Schedule scanning during low-activity periods to reduce visual clutter and ensure clarity in the captured data.
Most importantly, before scanning, always walk the site to identify obstacles and plan your approach. Use this time to map out scan paths that avoid obstructions, reflections, or areas that need extra care, like narrow spaces or shiny surfaces. Overall, get a sense of the scan area and density ahead of time so you’re prepared.
2. Capture your space with 3D scanning
High-fidelity 3D scanning is the cornerstone of an effective scan-to-BIM workflow. For professionals across the AEC industry—from architects and engineers to contractors and facility managers—accurate spatial data is essential for ensuring a smooth transition from physical spaces to actionable digital models. Matterport’s tools provide the precision and versatility required to capture data efficiently and effectively.
A 2022 study explored the potential of 3D scanning and highlighted a few best practices:
“The first step is to connect every part of the 3D Scanner, mount the right camera and projector lens combination, place the object scanned on the rotary table's focal point, and turn on the power. The blue light shows that the connections are OK; if the light does not glow, the connections and power supply should be examined again. The project information is then loaded into scanning software and set up according to the right lens, rotary table, calibration plate, etc.”
Best Practices:
Use the Matterport Pro3 Camera to capture LiDAR-enabled scans that deliver high accuracy for both indoor and outdoor spaces, demonstrating LiDAR applications in various environments. Its ease of use makes it ideal for detailed room mapping and large-scale site documentation alike.
Follow a systematic scanning pattern to ensure thorough coverage of the site. Overlapping scans can help fill in gaps and create a seamless dataset, reducing the need for manual corrections later.
Account for environmental factors, such as lighting and movement, to reduce noise and ensure the clarity of the captured data.
Ensure proper alignment of scans by marking reference points in complex environments. This step can streamline the processing phase and improve the overall quality of the model.
Closing this step successfully means having a comprehensive and clean dataset ready for processing. By leveraging Matterport’s user-friendly platform and advanced scanning capabilities, AEC professionals can significantly reduce rework, save time, and set the stage for a successful model generation phase.
3. Data processing and model generation
Once the scans are complete, data processing translates raw point cloud data into actionable BIM files and models.
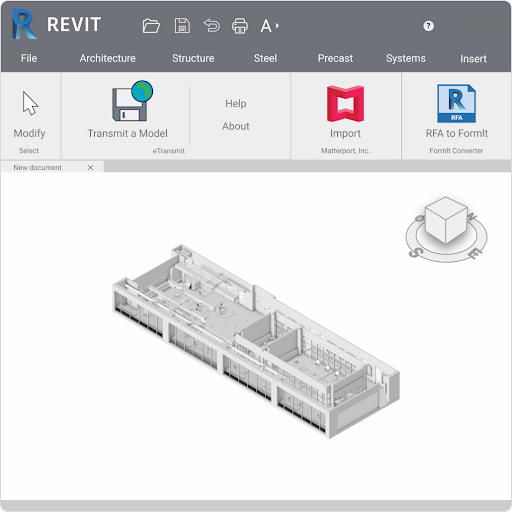
Best Practices:
Leverage MatterPak Add-On to access essential files like point clouds, OBJ files, and high-resolution floor plans, which integrate directly into BIM tools like Autodesk Revit or AutoCAD.
Use Matterport’s E57 file support for high-density point clouds, enabling millimeter-level accuracy in BIM model creation.
Validate processed models against captured point cloud data to ensure precision in the final output.
4. Model refinement and BIM creation
Refining the BIM model involves enhancing detail and integrating non-geometric data to meet project requirements.
Best Practices:
Create BIM models with an appropriate Level of Detail (LOD). Matterport’s workflows typically support LOD 200, suitable for initial project scoping.
Use Autodesk Revit or similar tools to fine-tune the model based on Matterport’s accurate point cloud inputs.
Streamline initial project scoping by leveraging pre-processed files for BIM clash detection and structural analysis.
Matterport’s cloud platform converts scans into practical formats—like point clouds, Revit models, and 2D floorplans—making it easy for project managers and contractors to access and share real-time, detailed spatial data. It eliminates the need for manual scan translation, giving you LOD 200 BIM files to kickstart documentation and design.
With this, your team can skip the heavy lifting upfront and get straight to scoping design requirements, knowing you have a reliable LOD 200 foundation.
1488 Stonebrook Lane, Lenoir City, TN 37772; Captured with Pro2
For larger or more complex scans, you can pair our Pro2 camera with integrations like Leica’s BLK360. This way, you can capture interior and exterior spaces. And, they support multiple sensors, i.e., they work for a variety of projects, from construction tracking to facility management.
5. Quality assurance and verification
Quality assurance ensures that the BIM model reflects the real-world conditions captured during scanning.
Case in point: Recent research shows that major construction projects around the world are running into serious cost and schedule overruns, with claims totaling over $91 billion and delays adding up to 876 years.
Best Practices:
Perform automated clash detection using BIM software integrated with Matterport’s point cloud data. This helps identify conflicts between MEP systems and structural elements early.
Conduct manual reviews of critical building systems to cross-verify accuracy.
Regularly compare as-built models to as-designed BIM models to ensure compliance with project requirements and safety codes.
6. Collaboration and model sharing
Collaboration is essential to maximizing the value of BIM models. Matterport’s cloud-based platform simplifies model sharing and stakeholder engagement.
Best Practices:
Use Matterport’s digital twin platform to share immersive 3D models, allowing remote stakeholders to explore spaces, annotate features, and make informed decisions.
Leverage cloud-based collaboration tools to enable real-time feedback and updates to the BIM model.
Ensure all stakeholders have access to the most up-to-date version of the model to minimize miscommunication.
7. Best practices to get scan-to-BIM process right
We’ve shared tips throughout each step of the scan-to-BIM workflow, but here’s a quick recap of best practices to help you get off to a good start:
Define the purpose of the workflow upfront
For renovations: Highlight capturing accurate as-built conditions for older buildings to streamline design planning.
For construction: Explain how ongoing scans can monitor progress and validate on-site conditions.
For facility management: Include how digital twins can be used for preventive maintenance or space optimization.
Automate what you can with tools like Matterport’s point cloud exports which integrate directly with Autodesk Revit or AutoCAD and saves time by eliminating the manual input step.
Pay extra attention to complex or heavily modified areas, since they need the highest level of accuracy — tools like the Matterport Pro3 Camera excel at capturing intricate environments where accuracy is key (eg. crowded mechanical rooms or heritage sites).
Keep detailed records of all scans, updates, and changes to avoid confusion — Matterport’s platform enables cloud-based record-keeping by providing accessible project documentation and annotated 3D scans for stakeholder collaboration.
Use point cloud-to-BIM for clash detection and better project accuracy — point cloud data can be integrated into BIM software for clash detection at the pre-construction stage; for example, detecting overlaps between HVAC systems and structural elements in the planning and design stage of a project to avoid future rework, saving time and cost.
Perform ongoing scans during key project milestones to keep the models up-to-date during the construction process and ensure that as-built conditions align with the design and project developments.
Catch potential clashes early by using scan data to spot issues between architectural, structural, and MEP systems before construction begins.
Incorporating data for long-term use by using IoT sensor integration or maintenance schedules in the BIM model for smart building management, making it a dynamic, long-term asset for facility owners.
By following these best practices, AEC companies can leverage reality capture to create highly accurate BIM models that streamline workflows, improve collaboration, and support smarter project outcomes. Whether it’s for renovation, construction, or long-term facility management, the right scan-to-BIM approach ensures every project stage is set up for success.
Matterport makes your scan-to-BIM process effortless
Matterport revolutionizes scan-to-BIM workflows by simplifying site documentation, planning, and collaboration for AEC professionals. By integrating seamlessly with tools like Autodesk Revit and AutoCAD, Matterport’s platform creates precise digital twins that provide an interactive and continuously accessible view of any space. With Matterport, you can capture data faster, process it seamlessly in the cloud, and collaborate remotely—eliminating the need for frequent site visits and saving valuable time.
How Matterport supports AEC workflows
Here are the 3 key ways in which Matterport improves the efficiency of existing AEC workflows:
Integration with BIM Tools: Export high-fidelity point clouds and models directly into Autodesk Revit or AutoCAD, streamlining your scan-to-BIM process.
Remote Walkthroughs: Use immersive digital twins to share updates, track progress, and make collaborative decisions without needing to visit the site physically.
Annotations and Tags: Enhance communication by tagging critical elements in the 3D model, ensuring everyone is aligned on project requirements.
Real-world success: Skipp Renovation Partners
San Francisco-based Skipp Renovation Partners partnered with Matterport to transform their preconstruction workflows, cutting homeowners’ renovation costs by over 50%.
“We’ve been using Matterport technology from the start,” says Jaffrey, co-founder of Skipp Renovation Partners. “With the 3D imagery and precise spatial data captured in digital twins, we dramatically transformed the preconstruction process.”
Discover how Matterport can simplify your scan-to-BIM process and deliver exceptional results for your AEC projects: sign up for a free account.